原因分析 |
處理辦法 |
燈板表面臟,硅膠與燈板表面助焊劑發(fā)生化學反應 |
-
焊接后,燈板需要清洗干凈;
-
在生產前,將燈板放入烤箱烘烤8-12小時,使燈板表面化學成份揮發(fā)。
|
硅膠未徹底硫化,產品放置在常溫下還在緩慢的硫化,導致空氣中的水份與其它物質與硅膠發(fā)生反應。 |
-
調慢隧道爐速度。
-
提高隧道爐溫度(不能超出產品承受溫度)。
-
嚴格按硫化劑添加比例添加,防止煉膠過程中灑落,導致硫化劑比例不足。
-
重復烘烤。
|
材料本身有質量問題 |
與硅膠、硫化劑、底涂劑廠商聯系解決。 |
原因分析 |
處理辦法 |
燈板表面受潮 |
燈板在擠出前,需經過烘烤除濕。 |
底涂未徹底烤干 |
加強烘烤 |
硅膠由于存放時間、煉膠方法等原因造成硅膠不良 |
更換硅膠,重新煉膠使用。 |
原因分析 |
處理辦法 |
擠出機未清洗干凈,死膠混入產品中 |
-
在停機后,將螺桿取出用酒精清潔干凈螺桿和螺筒。
-
在開機后,喂膠擠出,待膠從螺桿處出來后,切除螺桿頂端的3圈膠后再裝機頭。
|
煉膠機、工作臺面未清潔干凈 |
煉膠前請徹底清潔煉膠機與放膠工作臺。 |
煉好的硅膠放置時間太長 |
請嚴格控制煉好的膠的操作時間(參照煉膠機操作指南)。 |
原因分析 |
處理辦法 |
內模(外模)表面劃傷 |
重新拋光 |
外模口粘有死膠或異物 |
清理死膠或異物 |
原因分析 |
處理辦法 |
斷膠:一般發(fā)生在燈帶底部,原因為底部膠太薄或喂膠口斷膠,導致燈帶整體變細拉長。 |
-
調整燈帶底部膠厚度(請將底部膠厚度調整到0.8mm以上)。
-
擠出過程中,時刻注意機器進膠口,不可出現斷膠的情況。
|
新舊硅膠交替時,新舊膠硬度差異,導致擠出量不同,使燈帶尺寸不附合要求 |
在新舊膠交替時,密切關注擠出??跓魩У某叽纾瑢D出機速度進行動態(tài)調整。 |
原因分析 |
處理辦法 |
燈帶表面臟污 |
使用酒精將端子位擦試干凈,然后包膠。 |
模壓機壓力不足或燈帶有凹陷,使膠無法與燈帶緊密連接 |
-
調整氣壓,在空芯燈帶腔體內填膠。
-
選用更大口徑的氣缸,增大壓力(請選用原廠家配套設備)。
|
原因分析 |
處理辦法 |
燈珠為凹杯,在擠出時,膠體無法進入燈杯內。 |
做實芯擠出燈帶,目前為止,只能使用平杯封裝的燈珠,凹杯可用于擠出空芯燈帶。請更換平杯封裝燈珠后生產。 |
燈珠封裝膠為軟膠(硅膠),現有底涂劑無法使膠水與燈珠相粘。 |
做實芯擠出燈帶,目前只能用硅樹脂(硬膠)封裝的燈珠,現有底涂劑無法使硅膠與軟膠封裝燈珠相粘。請更換燈珠后生產 |
底涂劑與現有材料不兼容 |
不同廠家的板和燈珠,有可能會與現有的底涂劑不相粘的情況,請生產實芯燈帶前先進行首件測試后再批量生產。 |
原因分析 |
處理辦法 |
模具調整不到位 |
內模與外模之間的上下高度,前后距離都可能造成擠出燈帶底部膠面不平整,請重新按試橫標準調試內外模位置。 |
模具本身設計問題 |
重新設計模具(此問題在試模時即可發(fā)現,一般發(fā)生于全新結構模具上)。 |
-
擠出產品尺寸不穩(wěn)定(時大時?。?/span>
原因分析 |
處理辦法 |
膠條的尺寸偏差太大 |
煉好的膠在切條時,盡可能做到寬度厚度一致(誤差不應超過30%)。 |
喂料過程中斷料 |
喂料過程中,膠料的尺寸、方法要保持一致且連續(xù),出現斷料必然會導致產品尺寸不統(tǒng)一,當出現斷料時,請及時補上并將擠出速度略調大,使擠出產品尺寸一致,等料補齊后再調回擠出速度。 |
新舊膠料交替 |
新舊膠料交替時,由于放置時間的原因,膠料硬度會有一定差異(隨著環(huán)境溫度的升高,差異會更大),擠出機在同一速度時,擠出膠量會有變化。在每一次新舊膠料變更時,密切注意尺寸變化,以便調整擠出機速度進行補償。 |
原因分析 |
處理辦法 |
隧道爐溫度過高,導致燈珠虛焊 |
調低隧道爐溫度 |
燈珠本身質量問題,無法承受高溫 |
更換質量較好的燈珠 |
其它質量問題,請與我們進行溝通,我們將通過多方渠道協助你們將問題盡快解決,技術支持電話:18816855880。
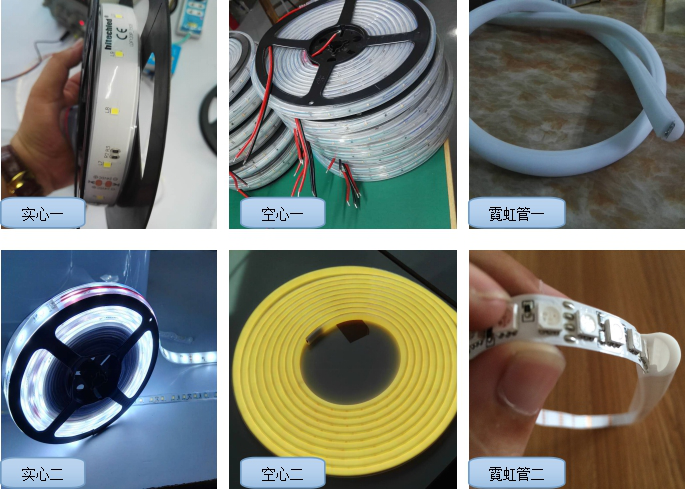